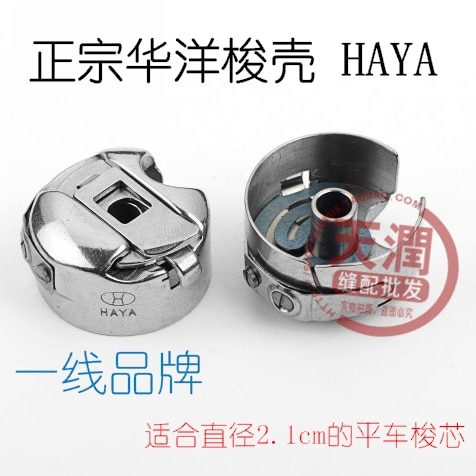
However, the 20% is multiplied times the fixture’s book value at the beginning of the year instead of the fixture’s original cost. The double declining balance method of depreciation, also known as the 200% declining balance method of depreciation, is a form of accelerated depreciation.
New hardware runs faster, uses less energy and provides more cores every year, likewise SaaS platforms often employ rapid upgrade cycles with a constant influx of improvements. In that context it doesn’t make sense to sink money into technology that could be obsolete by the very next model. The IRS makes a distinction between capital improvements and repairs.
What’s the difference between repair and maintenance?
Ordinary repairs are expenditures for repairs that do not prolong the life of an asset or increase its usefulness. If they had instead met one or both of the preceding criteria, repairs would instead be capitalized and charged to expense over time. An example of an ordinary repair is the replacement of a worn part on a machine.
This means that compared to the straight-line method, the depreciation expense will be faster in the early years of the asset’s life but slower in the later years. However, the total amount of depreciation expense during the life of the assets will be the same. Thus, the method is based on the assumption that more amount of depreciation should be charged in early years of the asset.
Non-routine maintenance includes maintenance that is performed reactively or only when needed based on an asset’s conditions. Scheduled maintenance includes work that is scheduled on a calendar for completion. The most common type of scheduled maintenance is calendar-based preventive maintenance tasks. For instance, an asset with a monthly PM has twelve instances of scheduled maintenance in a given year. However, just because maintenance is scheduled does not mean it’s planned.
Capital expenditures cover any major investments in goods which will show up on an organization’s balance sheet. Predictive maintenance (PdM) is what savvy maintenance teams aspire to have or are already implementing. The major barrier to PdM is the time it takes to implement rather than the cost of the technology itself.
Even a state of the art manufacturing plant that has predictive maintenance technology will use less advanced types of maintenance. Let’s assume that a retailer purchases fixtures on January 1 at a cost of $100,000. It is expected that the fixtures will have no salvage value at the end of their useful life of 10 years. Under the straight-line method, the 10-year life means the asset’s annual depreciation will be 10% of the asset’s cost. Under thedouble declining balance method the 10% straight line rate is doubled to 20%.
As an asset forays into later stages of its useful life, the cost of repairs and maintenance of such an asset increase. Hence, less amount of depreciation needs to be provided during such years. Depreciation is the accounting process of converting the original costs of fixed assets such as plant and machinery, equipment, etc into the expense. It refers to the decline in the value of fixed assets due to their usage, passage of time or obsolescence.
The “double” means 200% of the straight line rate of depreciation, while the “declining balance” refers to the asset’s book value or carrying value at the beginning of the accounting period. You need to determine a suitable way to allocate cost of the asset over the periods during which the asset is used.
Join PRO or PRO Plus and Get Lifetime Access to Our Premium Materials
In these challenging economic times, many organizations are in the pursuit of maintaining a lean balance sheet to preserve cash flow. As a result many organizations, including yours, may be paring back or freezing new CapEx investments, opting instead wherever possible to fund projects from OpEx budget. From a technology perspective, these decisions on what should or should not be a capital asset are also influenced by the rapid changes inherent in modern technology.
Generally, the method of depreciation to be used depends upon the patterns of expected benefits obtainable from a given asset. This means different methods would apply to different types of assets in a company. This method is a mix of straight line and diminishing balance method. Thus, depreciation is charged on the reduced value of the fixed asset in the beginning of the year under this method. However, a fixed rate of depreciation is applied just as in case of straight line method.
- Capital expenditures cover any major investments in goods which will show up on an organization’s balance sheet.
- Predictive maintenance (PdM) is what savvy maintenance teams aspire to have or are already implementing.
Ordinary versus major and extraordinary repair costs
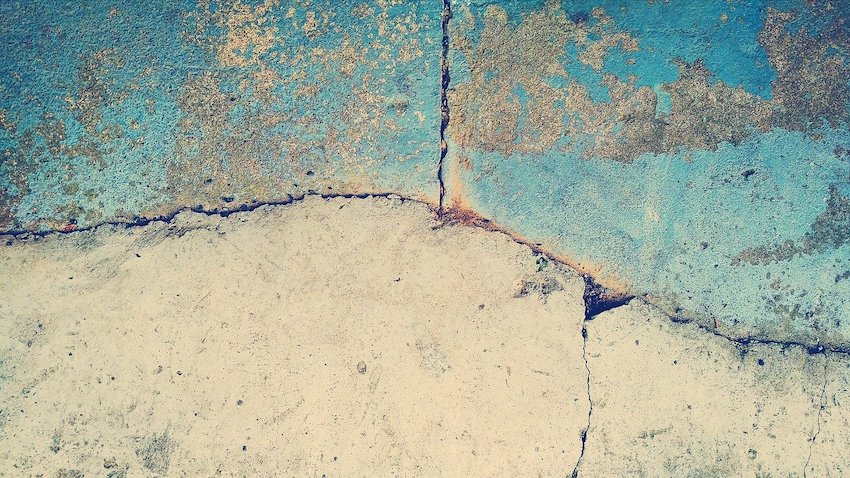
The IRS sets specific standards for an improvement to qualify as a cost-basis increase. A primary concern is it must be in place at the time a property is sold. Having a basic understanding of roof systems and the tangible property regulations can help building owners better evaluate the nature of the work performed. Careful analysis will produce a solid foundation for treating the cost of roofing work as either a repair expense or a capital improvement. A ‘Capital Expenditure’ is an acquisition or upgrade that permanently increases the value of an asset.
Accounting Topics
For instance, a vibration sensor that can identify imbalance, misalignment, and resonance issues only costs around $200. But the time it takes to install, integrate with other maintenance software, and adopt a culture around is not time that all organizations are willing to allocate. For those that do allocate the time, PdM provides an 8% to 12% cost savings over preventive maintenance. Preventive maintenance is the most popular type of proactive maintenance.
What is the difference between ordinary repairs and extraordinary repairs?
Ordinary repairs are expenditures for repairs that do not prolong the life of an asset or increase its usefulness. These expenditures are charged to expense as incurred.
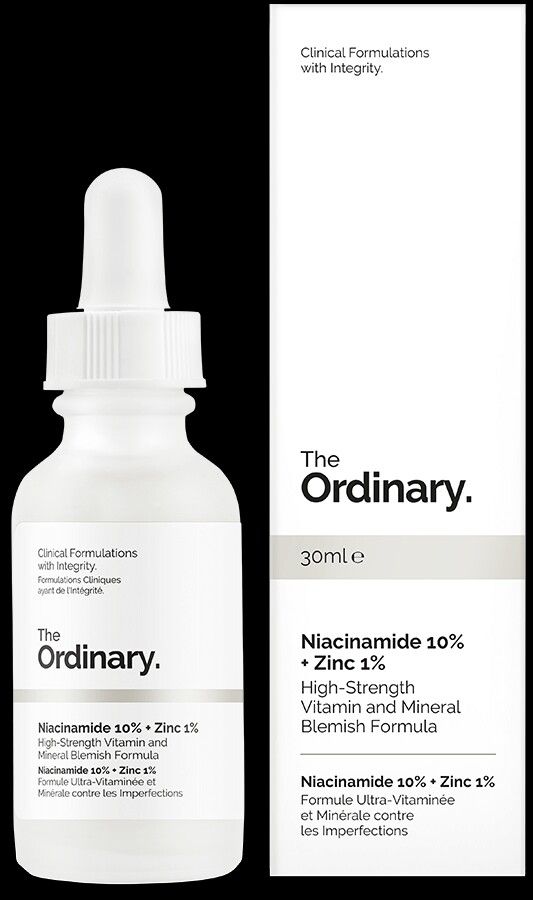
Repairs or maintenance cannot be included in a property’s cost basis. However, repairs that are part of a larger project, such as replacing all of a home’s windows, do qualify as capital improvements. Renovations that are necessary to keep a home in good condition are not included if they do not add value to the asset. Examples of such non-qualifying repairs, according to the IRS, include painting walls, fixing leaks, or replacing broken hardware.
Subsequent to the acquisition of fixed assets, a company may accrue costs for additions, improvements and replacements, rearrangements and reinstallations, maintenance and repairs of these assets. Repairs and maintenance are expenses a business incurs to restore an asset to a previous operating condition or to keep an asset in its current operating condition. The guidelines are pretty straightforward and we outline the process below. Routine maintenance is a form of time-based maintenance and preventive maintenance, though some organizations differentiate between routine maintenance and preventive maintenance. Additionally, routine maintenance is performed by operators, janitors, and other staff member while preventive maintenance is performed by technicians.
Repairs and maintenance expenses only maintain an asset’s life or current condition. The distinction is generally clear, although there are times when a judgement call is needed for a particular expense.
The costs of owning and operating your business vehicle are allowable business expenses. Since extraordinary repairs extend the life of the asset, they are not immediately expensed on theincome statementlike normal repairs are in the current year. Instead, extraordinary repairs arecapitalizedand reported on the balance sheet as an increase in value to the asset they upgraded.
To start conducting preventive maintenance tasks (PMs), an organization does not need to purchase new technology if it already has a CMMS. This is not the case with predictive maintenance which requires condition monitoring sensors and new software integrations. However, with preventive maintenance, the organization runs the risk of over-scheduling maintenance tasks because tasks are scheduled based on time rather than actual conditions. That said, preventive maintenance achieves 12% to 18% cost savings over reactive maintenance. Capital expenditures are costs that a company incurs to purchase an asset, extend its life, or increase its capacity or efficiency.