Assuming the company employs 10 laborers, and the minimum wage in the state of operation is $8, the company has a fixed cost of $80 per hour in the form of salaries. If it takes six hours for a laborer to make a dress with eight yards of fabric, then two laborers would make two dresses in 12 hours and use 16 yards of fabric. An increase in the number of dresses (production) means there must have been an increase in the number of laborers and the size of the fabric used.
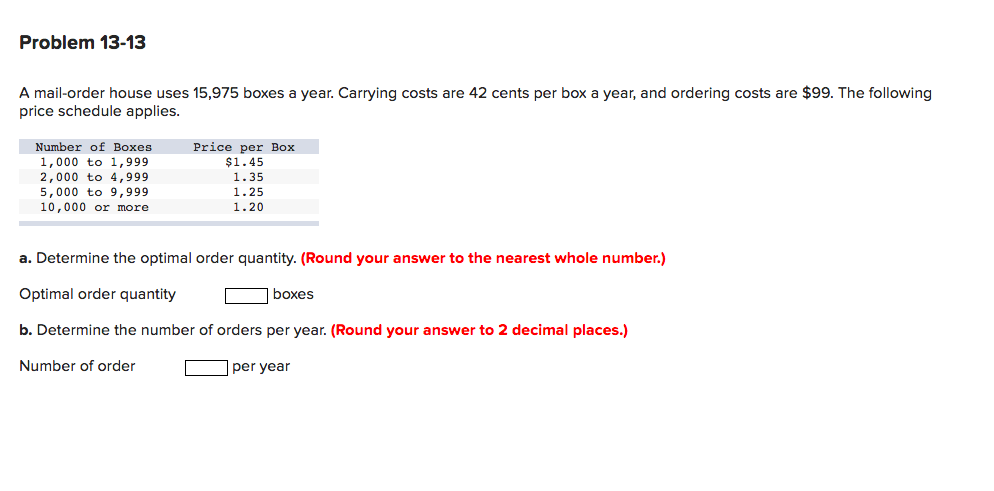
If you pay someone a mix of fixed salary plus commission, then they represent both fixed and variable costs. The cost of inventory is the “carrying cost” of holding and storing inventory over a certain period of time. It’s calculated to determine the amount of profit a business stands to gain.
Examples of Setup Costs
Also note that many cost items have both fixed and variable components. For example, management salaries typically do not vary with the number of units produced.
This includes warehousing costs such as rent, utilities and salaries, financial costs such as opportunity cost, and inventory costs related to perishability, shrinkage (leakage) and insurance. When there are no transaction costs for shipment, carrying costs are minimized when no excess inventory is held at all, as in a Just In Time production system. Business planning requires breaking expenses down into fixed and variable costs. Variable costs fluctuate according to the amount of output produced.
This can simplify decision-making, but can be confusing and controversial. Under full (absorption) costing fixed costs will be included in both the cost of goods sold and in the operating expenses. Fixed costs are not permanently fixed; they will change over time, but are fixed, by contractual obligation, in relation to the quantity of production for the relevant period. For example, a company may have unexpected and unpredictable expenses unrelated to production, such as warehouse costs and the like that are fixed only over the time period of the lease. By definition, there are no fixed costs in the long run, because the long run is a sufficient period of time for all short-run fixed inputs to become variable.
What is EOQ?
If you pay an employee a salary that isn’t dependent on the hours worked, that’s a fixed cost. Other types of compensation, such as piecework or commissions are variable. Semi-variable costs have elements of variable costs and fixed costs. Fixed costs remain the same, whether production increases or decreases. Economic order quantity (EOQ) is the ideal order quantity a company should purchase to minimize inventory costs such as holding costs, shortage costs, and order costs.
In business planning and management accounting, usage of the terms fixed costs, variable costs and others will often differ from usage in economics, and may depend on the context. Some cost accounting practices such as activity-based costing will allocate fixed costs to business activities for profitability measures.
Investments in facilities, equipment, and the basic organization that cannot be significantly reduced in a short period of time are referred to as committed fixed costs. Discretionary fixed costs usually arise from annual decisions by management to spend on certain fixed cost items. Examples of discretionary costs are advertising, insurance premia, machine maintenance, and research & development expenditures. In economics, fixed costs, indirect costs or overheads are business expenses that are not dependent on the level of goods or services produced by the business.
You can change a fixed cost – move to somewhere with lower rent, for instance – but the costs don’t fluctuate otherwise. Even if the economy craters and your sales drop to zero, fixed costs don’t disappear. In management accounting, fixed costs are defined as expenses that do not change as a function of the activity of a business, within the relevant period.
Conversely, the same high-fixed-costs company will experience magnification of profits because any revenue increases are applied across a constant cost level. Thus, as you can see in the example, fixed costs are an important part of profit projections and the calculation of break-even points for a business or project.
Carrying costs, also known as holding costs and inventory carrying costs, are the costs a business pays for holding inventory in stock. Even the cost of capital that helps to generate income for the business is a carrying cost. Employees who work per hour, and whose hours change according to business needs, are a variable expense. Piecework labor, where pay is based on the number of items made, is variable – so are sales commissions. If you must have a minimum number of employees to keep the sales office or the production line running, their pay may be a fixed cost.
- This can simplify decision-making, but can be confusing and controversial.
- In business planning and management accounting, usage of the terms fixed costs, variable costs and others will often differ from usage in economics, and may depend on the context.
This idea is also referred to as diminishing marginal cost.For example, let’s assume it costs Company XYZ $1,000,000 to produce 1,000,000 widgets per year ($1 per widget). This $1,000,000 cost includes $500,000 of administrative, insurance, and marketing expenses, which are generally fixed. If Company XYZ decides to produce 2,000,000 widgets next year, its total production costs may only rise to $1,500,000 ($0.75 per widget) because it can spread its fixed costs over more units. Although Company XYZ’s total costs increase from $1,000,000 to $1,500,000, each widget becomes less expensive to produce and therefore more profitable. In a factory that makes dresses, the variable costs are the fabric and the labor used to make the dresses.
Carrying costs are also sometimes referred to as the carrying costs of inventory. A company pays various costs over time for holding and storing inventory before it is sold and shipped to customers. Businesses calculate these costs to evaluate the level of profit they can reasonably expect on their current inventory. It is also useful in determining whether a company should increase or decrease the production of goods.
How to Manage Your Order and Setup Costs
It also helps you determine how much more or less inventory you need to satisfy demand. Some fixed costs change in a stepwise manner as output changes and therefore may not be totally fixed.
Conversely, when lot sizes decrease, inventory holding/carrying costs decrease, but the cost of ordering/setup increases since more orders/setups are required to meet demand. When the two costs are equal (holding/carrying costs and ordering/setup costs) the total cost (the sum of the two costs) is minimized. Cycle inventories, sometimes called lot-size inventories, result from this process. Usually, excess material is ordered and, consequently, held in inventory in an effort to reach this minimization point. Hence, cycle inventory results from ordering in batches or lot sizes rather than ordering material strictly as needed.
Improvement of warehouse or storage space may also be an option when trying to lower carrying costs. Having an efficient and cost-effective warehouse design and utilizing correct storage techniques can help keep carrying costs down. Businesses can reduce their carrying costs by implementing efficient warehouse design and by using computerized inventory management systems to keep track of inventory levels.
How do you calculate ordering cost?
Ordering costs are the expenses incurred to create and process an order to a supplier. These costs are included in the determination of the economic order quantity for an inventory item. Examples of ordering costs are: Cost of the labor required to inspect goods when they are received.
EOQ (Economic Order Quantity)
First of all, we need to go through the idea of economic order quantity (EOQ). EOQ is an attempt to balance inventory holding or carrying costs with the costs incurred from ordering or setting up machinery. The total cost will minimized when the ordering cost and the carrying cost equal to each other. While customer order a significant quantities of products, cycle inventory would be able to save cost and act as a buffer for the company to purchase more supplies. In marketing, carrying cost, carrying cost of inventory or holding cost refers to the total cost of holding inventory.
There are options business owners can implement to decrease the amount spent on carrying costs. They can also limit the amount of time the inventory spends in storage. For businesses that utilize refrigerated warehouse space, this tactic is of specific importance.
For example, a retailer must pay rent and utility bills irrespective of sales. In marketing, it is necessary to know how costs divide between variable and fixed costs. This distinction is crucial in forecasting the earnings generated by various changes in unit sales and thus the financial impact of proposed marketing campaigns. In a survey of nearly 200 senior marketing managers, 60 percent responded that they found the “variable and fixed costs” metric very useful.
By knowing its carrying costs, a business can stay on top of expenses and continue to generate a steady income stream. The difference between fixed and variable costs is essential to know for your business’s future. The amount of raw materials and inventory you buy and the costs of shipping and delivery are all variable. Fixed costs include rent, utilities, payments on loans, depreciation and advertising.
They tend to be time-related, such as interest or rents being paid per month, and are often referred to as overhead costs. This is in contrast to variable costs, which are volume-related (and are paid per quantity produced) and unknown at the beginning of the accounting year. On the other hand, the wage costs of the bakery are variable, as the bakery will have to hire more workers if the production of bread increases. Economists reckon fixed cost as an entry barrier for new entrepreneurs. When large quantities are ordered or produced, inventory holding costs are increased, but ordering/setup costs decrease.
Carrying Costs and Order Costs
This production-scheduling model was developed in 1913 by Ford W. Harris and has been refined over time. The formula assumes that demand, ordering, and holding costs all remain constant. A company with a relatively large amount of variable costs may exhibit more predictable per-unit profit margins than a company with a relatively large amount of fixed costs. This means that if a firm has a large amount of fixed costs, profit margins can really get squeezed when sales fall, which adds a level of risk to the stocks of these companies.