Inventory is either the finished goods stored and offered for sale by a business or the raw materials used by a company to produce finished products. An inventory control system is a process businesses use to manage inventory. Three general types of inventory control systems include continuous review systems, periodic review systems, and just-in-time inventory control. Inventory management can be very convenient if you know how to do it. The well-functioning system is a process of overseeing the flow of items into and out of your stock.
Inventory takes in account all of the assets a business uses to produce the goods it sells and determines the sale price for the stock. For indirect materials, debit the overhead account and credit the raw materials inventory asset account. At the end of the accounting period, the balance of the overhead account is allocated to the cost of goods sold and ending inventory. For direct materials, debit the work in process inventory account and credit the raw materials inventory account. If the production process is so short that it doesn’t make sense to use a work in process account, debit the finished goods inventory instead.
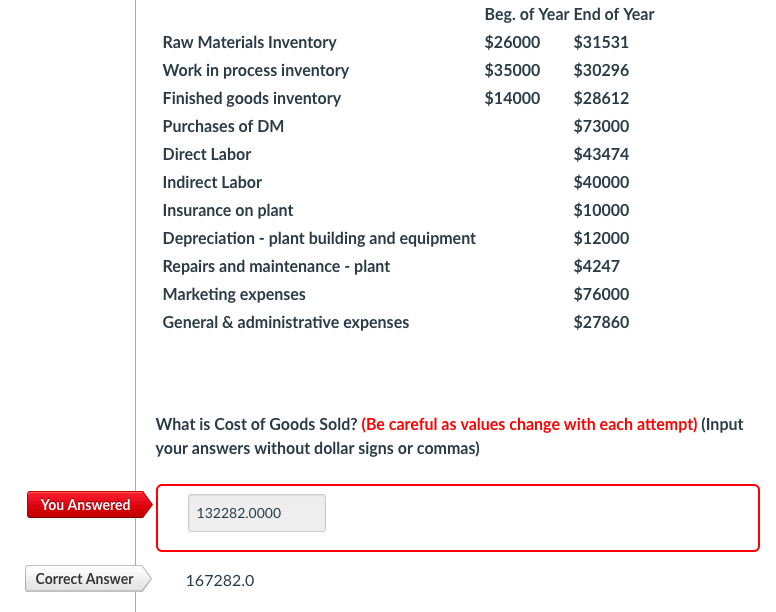
In other words, anything that goes into producing the items sold by your business is part of its inventory. All the products that surround you in your home, school, or workplace are made of one material or another. We’re surrounded by an incredible array of different materials every single day.
In other words, inventory represents finished goods or goods in different stages of production that a company keeps at its premises or at third-party locations with ownership interest retained until goods are sold. The three most important types of inventory are the raw materials, the work in progress (WIP) inventory and the finished goods. Raw materials are inventory items that are used in the manufacturer’s conversion process to produce components, subassemblies, or finished products. These inventory items may be commodities or extracted materials that the firm or its subsidiary has produced or extracted.
However, at the same time, your company also does not want to have too little inventory, as shortages can cost sales. This is because it can drive customers to other businesses that can meet their demands and can also decrease your business’s reputation by creating a dissatisfying experience for your customers.
If not used within a stipulated time limit, they can get expired and can’t be used in production. On the other hand, a company must have a certain minimum level of inventory at all times to cater to the production volumes, which mostly follow the trend of the market demand. Raw materials inventory is the total cost of all component parts currently in stock that have not yet been used in work-in-process or finished goods production. While stock deals with products that are sold as part of the business’s daily operation, inventory includes sale products and the goods and materials used to produce them. For example, the cars, car parts and accessories are sold during normal business practices, but the machines that run diagnostic tests on cars or the car lot itself are not.
AccountingTools
In addition, it must maintain some supply of finished goods in order to meet demand. Raw materials may sometimes be declared obsolete, possibly because they are no longer used in company products, or because they have degraded while in storage, and so can no longer be used.
Once the finished goods are sold, the cost of the raw materials should be recorded in the cost of goods sold account. Materials science is important for the development of technology and has been or thousands of years. Different materials have different strengths and weaknesses and are better for different purposes. Since technology is the process of using our scientific knowledge to create devices and objects that benefit humans, understanding materials is an important step in this process. Inventory is a quantity of goods owned and stored by a business that is intended either for resale or as raw materials and components used in producing goods that the business sells.
Types of Inventory
They are the raw materials that have been taken out of the raw materials store and are now undergoing the process of their conversion into the final products. These are the partly processed raw materials lying on the production floor. And they have also not reached the stage where they have been converted into the final product. Inventory means those current assets, which have been or will be converted into the final products of a company for sale in the near future.
They also include any kind of securities that a stock broker or dealer buys and then sells. Excess inventory, however, can also become a liability, as it may cost resources to store, and it may have a limited shelf life, meaning it can expire or become out of date. Examples include food which can eventually spoil, computers which can become obsolete, securities that lose too much of their value, or clothing that can go out of style or become no longer fashionable.
- An inventory control system is a process businesses use to manage inventory.
- Three general types of inventory control systems include continuous review systems, periodic review systems, and just-in-time inventory control.
- Inventory is either the finished goods stored and offered for sale by a business or the raw materials used by a company to produce finished products.
Your business may be forced to either dispose of these assets or sell them at a loss. Therefore, to keep inventory from becoming a liability or loss, a business must not store too much at any time.
TRANSIT INVENTORY
Inventories are the assets that will be of have been converted to the final products of a company. They are of three major types, namely raw materials, work in progress and finished goods.
BUFFER INVENTORY
The management of inventory calls for an optimum level of inventory that can be maintained by creating an inventory purchasing plan as per the strategy adopted by the company. This is because if a company keeps too much of raw material inventory in stock, it will incur higher carrying costs and there is also the undesirable possibility of the inventory getting obsolete. For example, in the pharmaceutical or food industry, the raw materials may be perishable.
If so, they are typically charged directly to the cost of goods sold, with an offsetting credit to the raw materials inventory account. In some cases, stock is also raw materials, if the business also sells those products to its customers. For example, a car dealership’s stock includes cars, but also can include tires, engine parts or other car accessories. Inventory includes a small business’s finished products, as well as the raw materials used to make the products, the machinery used to produce the products and the building in which the products are made.
MRO GOODS INVENTORY
For example, motherboards warehoused at a computer company to be used in the assembling of its computer systems are inventory. The products displayed for sale and stored in the backrooms of a department store are inventory as well. Work in progress inventory can also be called semi-finished goods.
Effective inventory management keeps the stock costs under control so you can run a successful business. These methods are used to manage assumptions of cost flows related to inventory, stock repurchases (if purchased at different prices), and various other accounting purposes. Inventory assets are goods or items of value that a company plans to sell for profit. These items include any raw production materials, merchandise, and products that are either finished or unfinished.
However, items such as nuts and bolts, ball bearings, key stock, casters, seats, wheels, and even engines may be regarded as raw materials if they are purchased from outside the firm. These goods are maintained on hand at or near a business’s location so that the firm may meet demand and fulfill its reason for existence. If the firm is a retail establishment, a customer may look elsewhere to have his or her needs satisfied if the firm does not have the required item in stock when the customer arrives. If the firm is a manufacturer, it must maintain some inventory of raw materials and work-in-process in order to keep the factory running.
They also may be objects or elements that the firm has purchased from outside the organization. Even if the item is partially assembled or is considered a finished good to the supplier, the purchaser may classify it as a raw material if his or her firm had no input into its production. Typically, raw materials are commodities such as ore, grain, minerals, petroleum, chemicals, paper, wood, paint, steel, and food items.
What are the 4 types of inventory?
Raw materials inventory is the total cost of all component parts currently in stock that have not yet been used in work-in-process or finished goods production. There are two subcategories of raw materials, which are: Direct materials. These are materials incorporated into the final product.