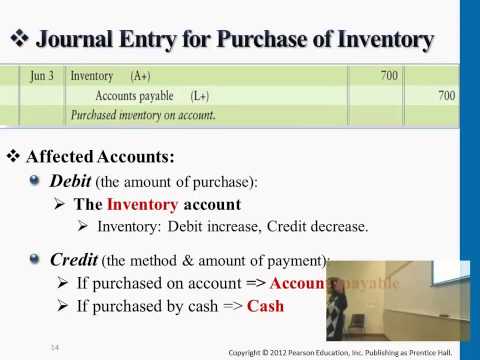
Cycle inventories, sometimes called lot-size inventories, result from this process. Usually, excess material is ordered and, consequently, held in inventory in an effort to reach this minimization point.
Inventory is needed to calculate cost of goods sold on a business tax form. Inventory costs reduce business income and business taxes. This is the end-of-year inventory done by many retailers.
The EOQ formula inputs make an assumption that consumer demand is constant. The calculation also assumes that both ordering and holding costs remain constant. Inventory assets are goods or items of value that a company plans to sell for profit.
Just-in-Time Inventory
The costs of its inventory include holding and setup costs. Holding costs associated with storing inventory are a major component of supply chain management because businesses must determine how much to keep in stock.
The EOQ formula assumes that consumer demand is constant. Economic order quantity (EOQ) is the ideal order quantity a company should purchase to minimize inventory costs such as holding costs, shortage costs, and order costs. This production-scheduling model was developed in 1913 by Ford W. Harris and has been refined over time. The formula assumes that demand, ordering, and holding costs all remain constant. Those who are familiar with the concept of economic order quantity (EOQ) know that the EOQ is an attempt to balance inventory holding or carrying costs with the costs incurred from ordering or setting up machinery.
What is inventory and example?
Inventory is a quantity of goods owned and stored by a business that is intended either for resale or as raw materials and components used in producing goods that the business sells. For example, motherboards warehoused at a computer company to be used in the assembling of its computer systems are inventory.
You must create an account to continue watching
When you sell the items, kpi.com Accounts credits the Stock asset account and debits the Materials Purchased, cost of goods sold account. The EOQ formula is best applied in situations where demand, ordering, and holding costs remain constant over time. The most important thing to know about inventory is that it’s essential in calculating the cost of goods sold (COGS). COGS is used to determine gross profit for a business that sells products, and it’s used on every business tax form, for sole proprietorships, partnerships, LLC’s, and corporations. FIFO valuation measures inventory by assuming that items that are in inventory first are sold first (even if this isn’t necessarily the case).
Generally speaking, ERP inventory management systems are best suited to medium or large businesses. This is because ERP systems are built for handling complex inventory and sales order processes, which usually apply to larger companies. The economic order quantity (EOQ) model is used in inventory management by calculating the number of units a company should add to its inventory with each batch order to reduce the total costs of its inventory.
Whether your business uses LIFO or FIFO depends on your business type and IRS regulations. Businesses take inventory so they know how much they have on hand at a specific point in time. Inventory includes both finished products, work-in-process (products in various stages of completion), and products to be used to make new sales items (called).
Hence, cycle inventory results from ordering in batches or lot sizes rather than ordering material strictly as needed. Inventory is either the finished goods stored and offered for sale by a business or the raw materials used by a company to produce finished products. An inventory control system is a process businesses use to manage inventory. Three general types of inventory control systems include continuous review systems, periodic review systems, and just-in-time inventory control.
Examples include food which can eventually spoil, computers which can become obsolete, securities that lose too much of their value, or clothing that can go out of style or become no longer fashionable. Your business may be forced to either dispose of these assets or sell them at a loss. Therefore, to keep inventory from becoming a liability or loss, a business must not store too much at any time. However, at the same time, your company also does not want to have too little inventory, as shortages can cost sales. This is because it can drive customers to other businesses that can meet their demands and can also decrease your business’s reputation by creating a dissatisfying experience for your customers.
- The calculation also assumes that both ordering and holding costs remain constant.
- Inventory assets are goods or items of value that a company plans to sell for profit.
- The EOQ formula inputs make an assumption that consumer demand is constant.
Inventories appear on a company’s balance sheet as an asset. Inventory turnover, which indicates the rate at which goods are converted into cash, is a key factor in appraising a firm’s financial condition.
The EOQ model seeks to ensure that the right amount of inventory is ordered per batch so a company does not have to make orders too frequently and there is not an excess of inventory sitting on hand. It assumes that there is a trade-off between inventory holding costs and inventory setup costs, and total inventory costs are minimized when both setup costs and holding costs are minimized.
Fluctuation in the ratio of inventory to sales is known as inventory investment or disinvestment. When you purchase and receive items, kpi.com Accounts credits the Pending Goods Received Notes account and debits the Stock asset account. When you convert this Purchase order to purchase invoice it credits the Accounts Payable account for the supplier and debits the Pending Goods Received Notes account.
These items include any raw production materials, merchandise, and products that are either finished or unfinished. They also include any kind of securities that a stock broker or dealer buys and then sells. Basically, inventory assets are your saleable inventory. Excess inventory, however, can also become a liability, as it may cost resources to store, and it may have a limited shelf life, meaning it can expire or become out of date.
When large quantities are ordered or produced, inventory holding costs are increased, but ordering/setup costs decrease. Conversely, when lot sizes decrease, inventory holding/carrying costs decrease, but the cost of ordering/setup increases since more orders/setups are required to meet demand. When the two costs are equal (holding/carrying costs and ordering/setup costs) the total cost (the sum of the two costs) is minimized.
Inventory management is the part of supply chain management that aims to always have the right products in the right quantity for sale, at the right time. When done effectively, businesses reduce the costs of carrying excess inventory while maximizing sales. Good inventory management can help you track your inventory in real time to streamline this process.
LIFO valuation assumes that items in inventory last are sold first. Average cost is, as it says, an average of the cost of all items sold in a period of time.
The cost of selling your inventory (called cost of goods sold) is an important cost for your business. It includes the cost of buying those products, raw materials, and component parts. It also includes costs of warehousing (storing) inventory, shipping products to customers, running a storage facility or warehouse, and hiring people to work in the warehouse.
Inventory
With key updates on stock, orders, and customers in a single location, ERP inventory management enables quality data collection. Most systems will also allow you to create and save custom inventory and sales reports to track business performance and plan for growth. Ordering a large amount of inventory increases a company’s holding costs while ordering smaller amounts of inventory more frequently increases a company’s setup costs. The economic order quantity model finds the quantity that minimizes both types of costs. To calculate the economic order quantity for inventory you must know the setup costs, demand rate, and holding costs.